There’s a slew of technology and tools to help streamline your system, add efficiencies to…
What is a Manufacturing Execution System (MES) and Why Does It Matter?
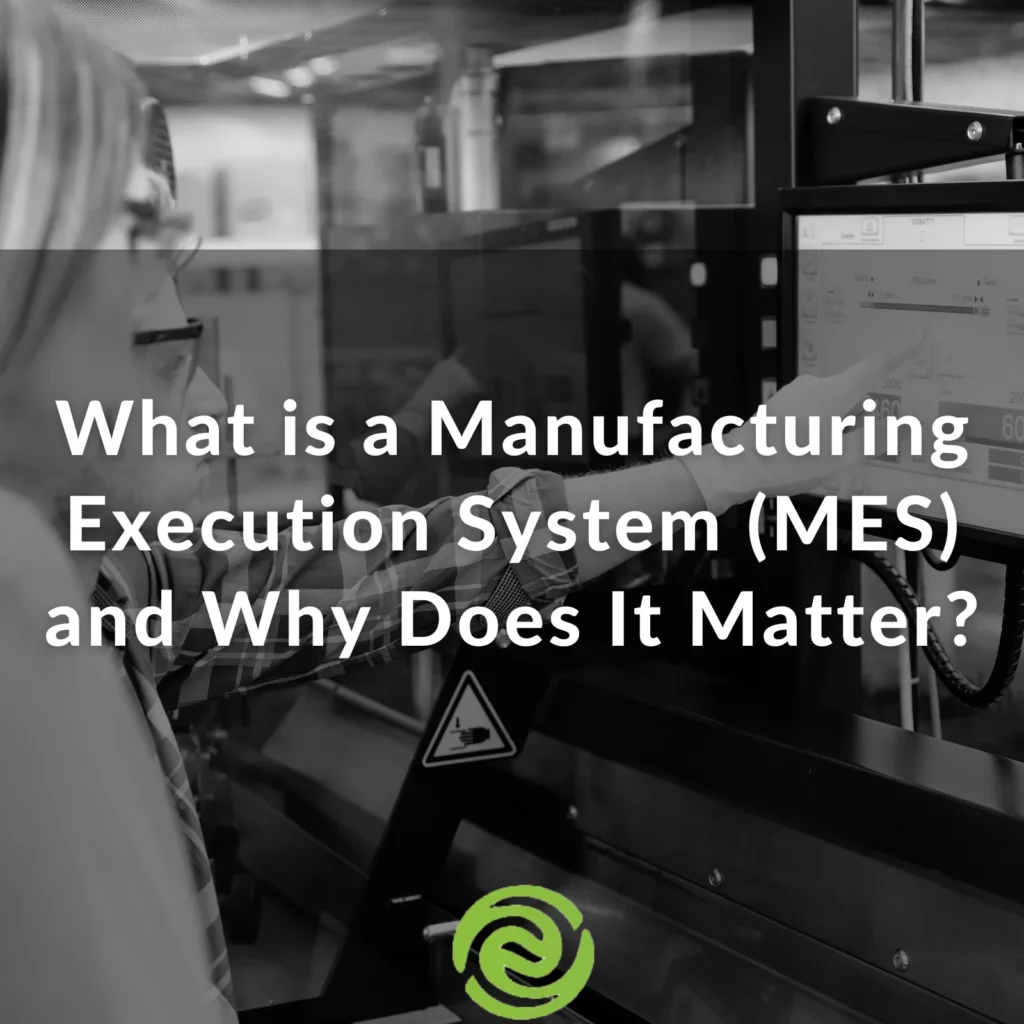
In the modern manufacturing landscape, companies are facing unprecedented pressures to increase productivity, maintain product quality, and reduce operational costs. As manufacturers grow or scale, these challenges multiply, making it harder to manage complex operations with manual systems or basic software. This is where a Manufacturing Execution System (MES) becomes vital—not as a luxury, but as an essential tool for manufacturers looking to stay competitive, minimize human error, and reduce overall costs.
What Exactly is an MES?
At its core, an MES is software that connects directly to your machines and operators to gather real-time data on various aspects of the manufacturing process. This data includes cycle times, downtime, material usage, production output, and maintenance notifications — all displayed via operator panels, and dashboards throughout the facility. With this level of transparency, facility floor managers can derive critical insights into what’s working well and where there is room for improvement in the overall equipment effectiveness (OEE).
This system doesn’t just track one machine but integrates all machines, providing a holistic view of the entire manufacturing process. Whether it’s determining your total cost per part or monitoring quality metrics, an MES acts as the “eyes” and “ears” for your operation, ensuring you can identify inefficiencies and areas for improvement quickly.
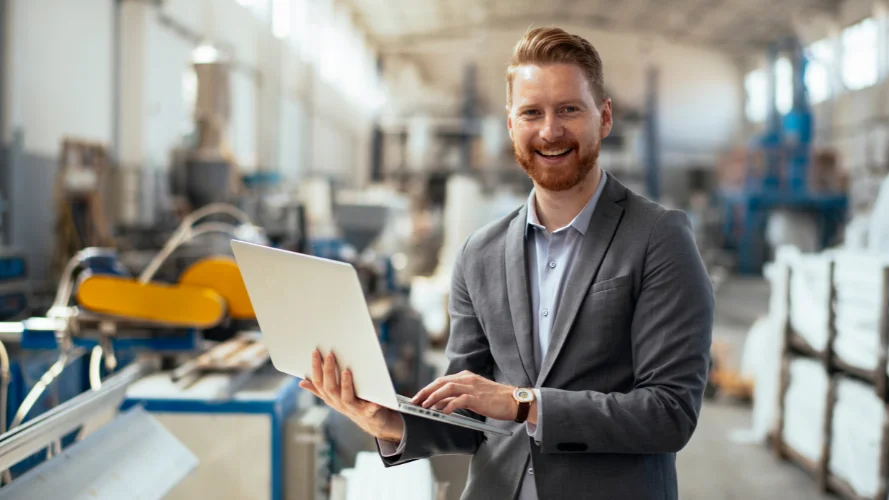
Key Benefits of an MES
Implementing an MES delivers substantial benefits to manufacturers, especially those seeking to optimize their operations and scale production efficiently. Here’s a closer look at the key benefits an MES provides:
- Measure Overall Equipment Effectiveness (OEE):
OEE is a critical metric that tracks how well your equipment is performing to identify areas for improvement. An MES tracks OEE by monitoring the availability, performance, and quality output of machines in real-time. By measuring OEE, manufacturers can easily identify underperforming areas and take swift corrective action, ensuring that machines are running at peak efficiency. - Measure Total Effective Equipment Performance (TEEP):
TEEP goes beyond OEE by measuring the utilization of your equipment based on its full potential over time. This allows the facility manager to get a broader picture of how effectively your facility is utilizing its equipment. This allows for long-term planning, helping manufacturers identify areas for improvement not only during production shifts but across the entire calendar of equipment usage. - Increased Visibility: MES offers unparalleled visibility into the production process, allowing managers to monitor and optimize machine utilization in real-time. This comprehensive visibility allows facility managers to make data-driven decisions, quickly resolve bottlenecks, and enhance communication between teams, leading to smoother production runs and fewer delays.
- Cost Per Part Calculations: By tracking material usage and machine performance, MES helps calculate the exact cost per part, making it easier to control production expenses from pricing, inventory management and overall production planning.
- Improved Traceability: For manufacturers operating in regulated industries like food, pharmaceuticals, or aerospace, traceability is non-negotiable. MES systems provide an automated way to track and document the production process, from raw material inputs to finished goods. This traceability is critical for ensuring compliance with regulatory standards, and it helps manufacturers respond quickly to audits, quality issues, or recalls.
- Enhanced Product Quality: Quality control is a major concern for manufacturers, especially those working in high-precision industries. An MES ensures that issues can be identified and corrected immediately. This reduces the number of defective products, minimizes rework, and helps maintain a high standard of quality across all production runs.
- Regulatory Compliance: An MES helps ensure compliance by automatically tracking the production process and generating supporting documentation. This makes it easier to meet industry standards and pass inspections, saving manufacturers time and reducing the risk of fines or penalties.
- Data-Driven ERP Integration: MES systems feed real-time data into ERP (Enterprise Resource Planning) systems through APIs, enabling better forecasting, planning, and resource allocation. This seamless integration ensures that data flows freely between the facility floor and the business side, helping manufacturers streamline operations from production to shipping.
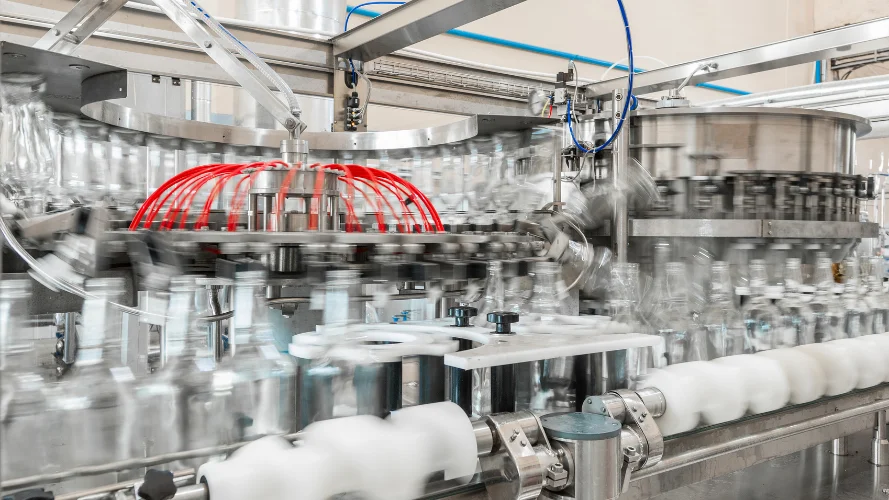
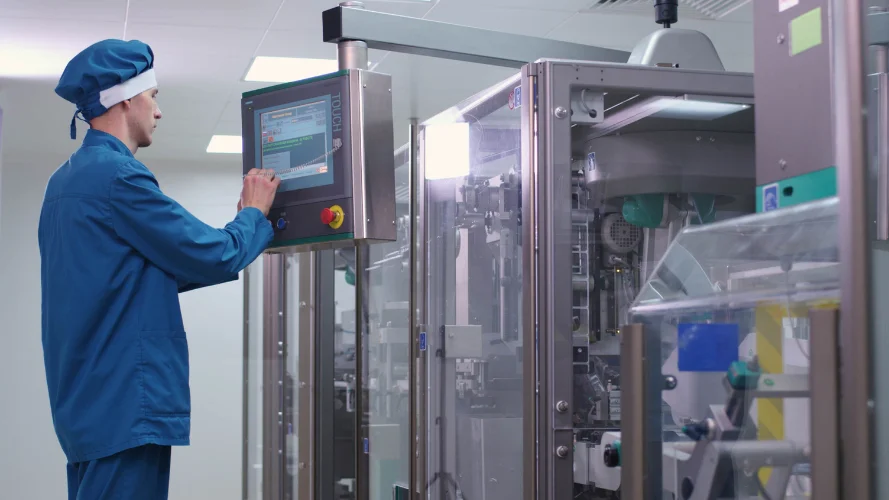
Why You Need an MES
Many manufacturers still rely on outdated manual systems or basic software that lacks the depth of insight necessary for modern manufacturing processes. Others may view MES as more of a luxury than a necessity. However, for manufacturers of a certain size or those planning for growth, an MES is essential to scaling and remaining competitive.
When thinking about adopting a Manufacturing Execution System (MES), it’s essential to understand that it’s not just about improving a few metrics—it’s about completely transforming how you utilize your most valuable resources. Beyond the key benefits of reducing downtime and improving quality, an MES ensures you’re getting the most out of your machines, materials, and workforce. It tracks and optimizes every part of your production process instantly, allowing you to reduce waste, increase efficiency, and avoid costly errors.
For manufacturers looking to scale, this level of resource utilization is critical. With an MES, you can run operations more efficiently, even 24/7, without needing to add extra shifts or hire more staff. The system automates much of the monitoring and decision-making, allowing you to maintain standards and reliability without human intervention—helping you save on labor costs while maintaining peak production levels. An MES is not just a tool to improve productivity, but a strategic solution for manufacturers who want to future-proof their operations and ensure long-term growth.
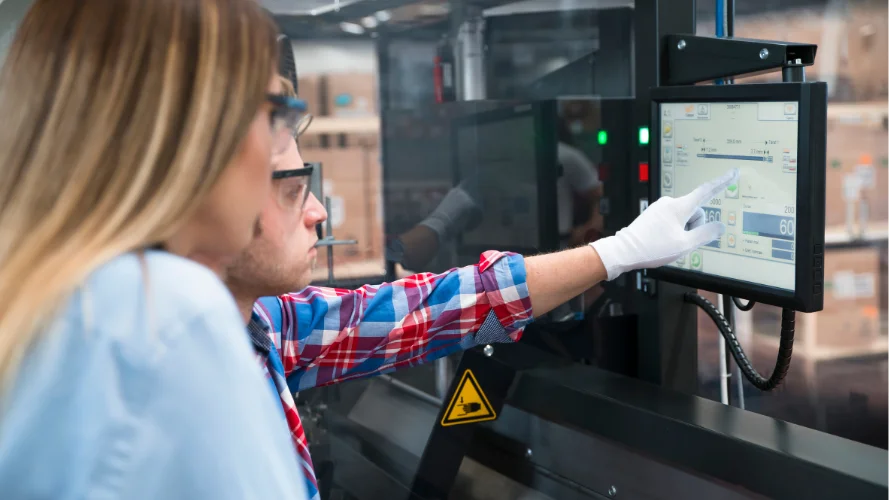
The Bottom Line… MES is a Necessity for Growth
In short, MES is more than just a luxury—it’s a necessity for manufacturers looking to stay competitive in today’s data-driven world.
Without an MES, your operations lack the transparency and real-time insight needed to optimize machine performance, manage resources efficiently, and maintain compliance.
At Swip Systems, we specialize in helping manufacturers adopt and integrate MES solutions into their existing operations. From evaluating your current system to implementing the right MES for your needs, we’re with you every step of the way. Our team works closely with your operators and IT staff to ensure a seamless transition, providing ongoing support and training to help you get the most out of your MES.
By partnering with Swip Systems, you can gain more control over your manufacturing operations, leading to better efficiency, higher quality, and increased profitability. Contact us today to learn how we can help you modernize your plant floor with a state-of-the-art MES solution.